How to make container shipping safer again
This is already the second winter that the shipping industry is experiencing a sharp rise in containers lost at sea. Experts at GDV have analysed the causes of this development and are proposing possible solutions.
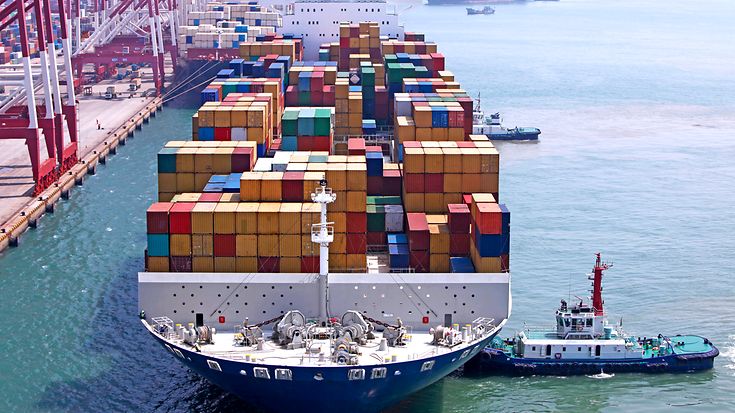
While containers used to be arranged in stacks of four to six layers, they are nowadays stowed in “towers” of up to 12 boxes.
The number of containers going overboard has increased dramatically in the last two years. The winter of 2020/21 saw cargo losses to the tune of hundreds of millions of euros. And this winter isn’t shaping up to be any better: In October, the ZIM Kingston lost more than 100 containers and caught fire as a result of the cargo loss; in November, the COSCO Nagoya had 38 containers falling overboard.
„We have to put a stop to this development: Cargo losses pose a threat to both the crew and the ship, they are expensive and they contribute to marine pollution”, says Anja Käfer-Rohrbach, Deputy CEO of GDV.
Security experts at GDV have analysed the causes of those numerous container losses and developed possible solutions. “The main problem is that the common practices for lashing and securing containers are no longer compatible with the sailing characteristics of large container ships”, Käfer-Rohrbach explains.
These are the causes and remedies the GDV’s experts propose:
1. Use anti-roll tanks and don’t load ships to capacity
Container ships have grown bigger and bigger in recent years. Some of them are more than 60 meters in width, making them highly stable; they tend to right themselves very quickly. If such a vessel is loaded to capacity, it is prone to dangerous lateral oscillation (“rolling”) in heavy seas – even when the ship doesn’t sail parallel to the waves but takes them head on. At the same time, container stacks of up to 12 boxes represent large windage areas on deck, which puts an additional strain on the cargo securing systems.
Anti-roll tanks can counteract dangerous roll motions. Ballast water flows back and forth in those tanks, damping the vessel’s rolling oscillation. However, such tanks are not mandatory and few shipping companies have them installed in their vessels. Therefore, the only short-term remedy is to reduce the number of containers on deck, because on ships that are not loaded to capacity, cargo losses are extremely rare.
2. Improve lashing and securing of containers on deck
Container ships have been carrying more and more boxes on deck. However, the cargo securing systems haven’t evolved accordingly. The standard container itself has seen very little improvement, too – even though containers are not arranged in four to six layers any more, like in the past, but stacked in towers up to 12 boxes high.
This requires a fundamental redesign of securing systems. They need to be updated and extended to fit the seakeeping characteristics of large and highly stable modern container ships – even when the vessels are operating at 100% capacity.
3. Check weight and quality of containers
While the weight of each and every container must be declared, there are no effective checking mechanisms in place. Seeing as the weight should determine where a container is stowed on board, this is most unfortunate. The heaviest boxes must invariably go to the bottom; the higher up a container is placed, the lighter is has to be. A single box that is too heavy or stowed incorrectly can overwhelm the cargo securing system of the entire stack. Sooner or later that loose stack will lean against a neighbouring stack and destroy its securing system, triggering a domino effect. Also, the quality of the containers must be right, because the boxes at the bottom muss support the weight of all the containers stacked on top of them.
Effective checking mechanisms will need to be implemented in order to detect incorrect weight declarations and avoid incorrect stowage. First, the weight must be verified. Second, a container’s quality and structural security need to be checked. Third, someone needs to make sure the cargo inside the container is stowed and secured correctly; otherwise that cargo will move around inside the box like a wrecking ball, overwhelming the securing system of the entire stack – which, in turn, will result in the domino effect described above.